Some cosmetics
Yes, I know cosmetics should come later but I am using the tractor for cutting thelawn grass and I could not stick the steering wheel centre cover missing, so I splashed out and bought a brand new one for about 25€. And cleaned the manky steering wheel. Looks much better now, I think. 
Also the cover under the dash board was held by a coach screw on one side. Really bugged me having to get a screw driver every time I wanted to take the cover off. So I bought 5 of those knob screws M6x20 for 6 quid on ebay (original is M6x15), fitted a DIN 1440 big washer over it and a soft padding cut from a cork/rubber gasket material. Love it !
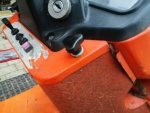
Yes, I know cosmetics should come later but I am using the tractor for cutting the
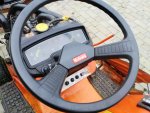
Also the cover under the dash board was held by a coach screw on one side. Really bugged me having to get a screw driver every time I wanted to take the cover off. So I bought 5 of those knob screws M6x20 for 6 quid on ebay (original is M6x15), fitted a DIN 1440 big washer over it and a soft padding cut from a cork/rubber gasket material. Love it !
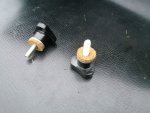
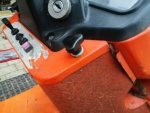
Last edited: