torch
Well-known member
Equipment
B7100HSD, B2789, B2550, B4672, 48" cultivator, homemade FEL and Cab
I started with 2x6 .188 wall rectangular tube for the side rails, and rounded up the bottom corners. I took some time to make sure these welds are tight, as I plan to fill the rails with WWF for additional weight if needed:
Some 3-1/2" x 2-1/2" x 1/4" angle iron looks like a nice cutting angle, and will support a piece of 3" x 3/8" flat bar.
I ground the edges not-quite-sharp, and slotted the holes (at the appropriate angle) for adjustment.
I've seen everything from 5° to 30° suggested as the appropriate angle. I picked 10°. It looked "right" to me. But then, what the heck do I know? I've never used one -- for that matter, I didn't even know what a land plane was a year ago. Your Mileage May Vary.
The angles for the hitch were easier to figure: I just copied my snowblower's dimensions:
And finally, I turned some pins for the lift arms. Now for some testing and paint:
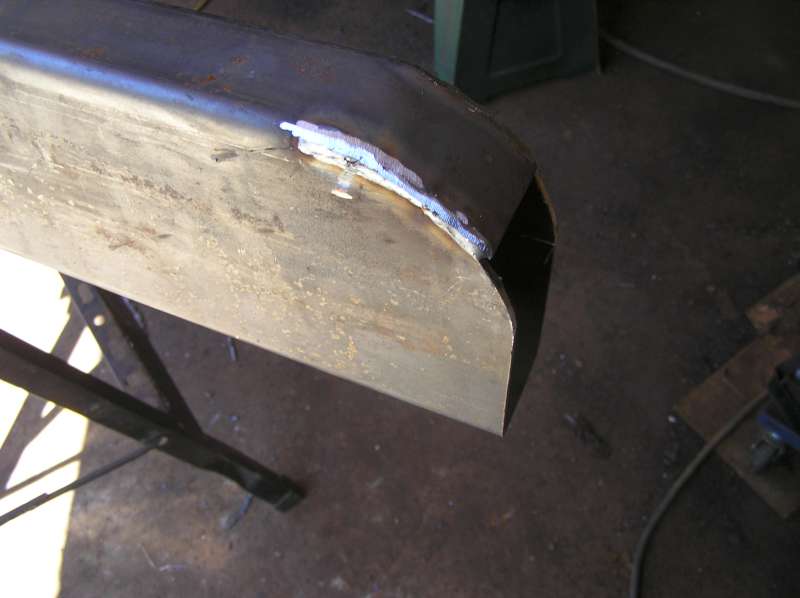
Some 3-1/2" x 2-1/2" x 1/4" angle iron looks like a nice cutting angle, and will support a piece of 3" x 3/8" flat bar.
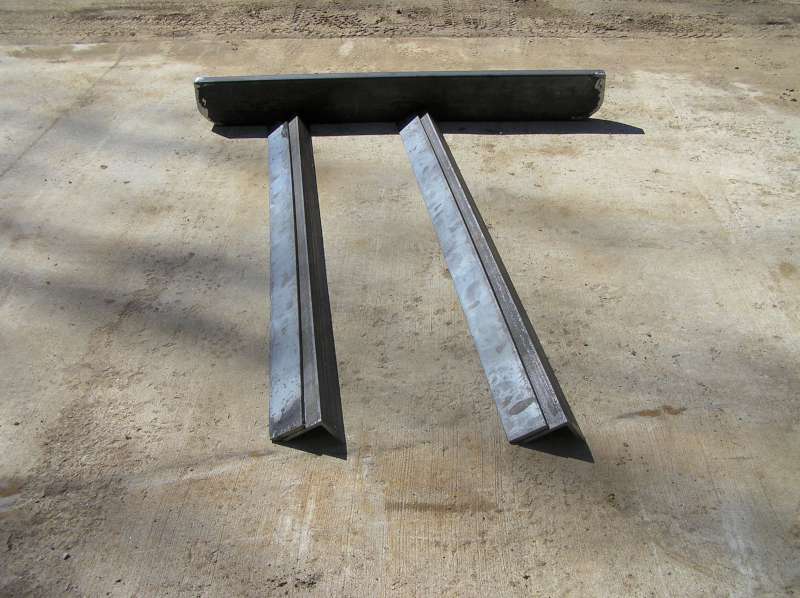
I ground the edges not-quite-sharp, and slotted the holes (at the appropriate angle) for adjustment.
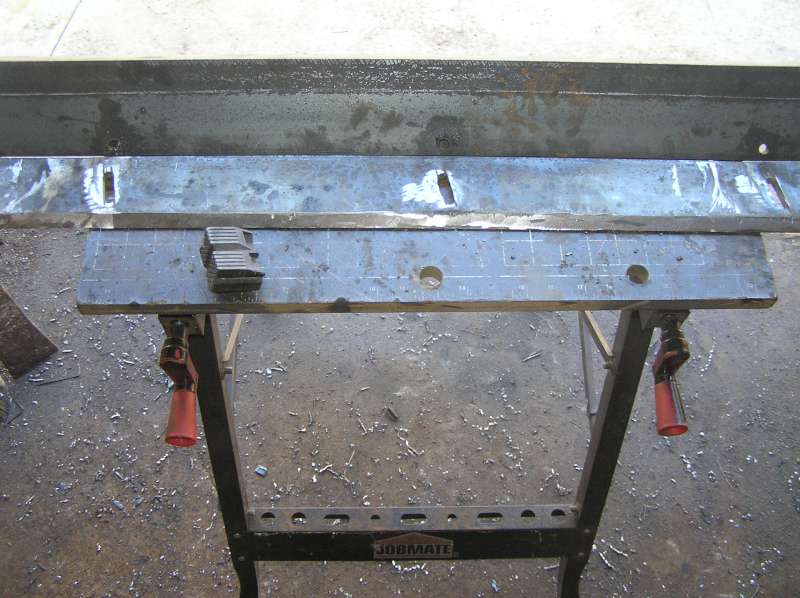
I've seen everything from 5° to 30° suggested as the appropriate angle. I picked 10°. It looked "right" to me. But then, what the heck do I know? I've never used one -- for that matter, I didn't even know what a land plane was a year ago. Your Mileage May Vary.
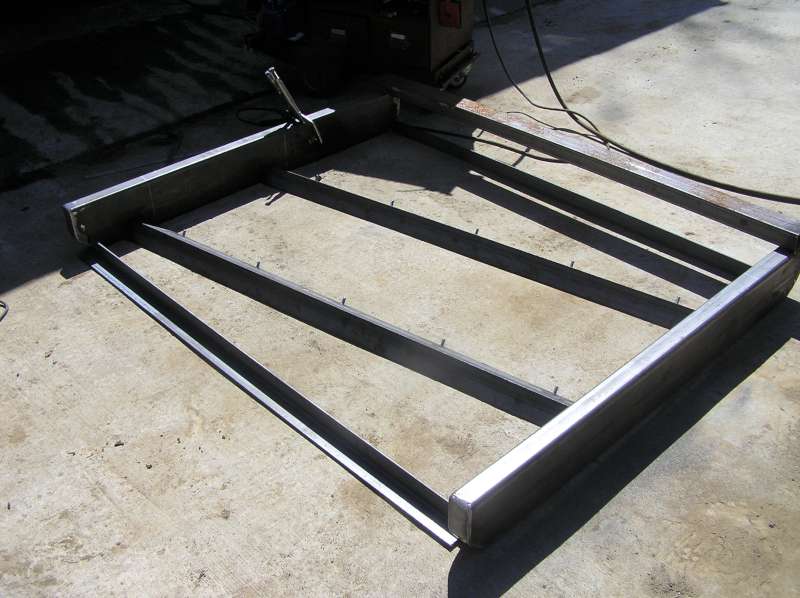
The angles for the hitch were easier to figure: I just copied my snowblower's dimensions:
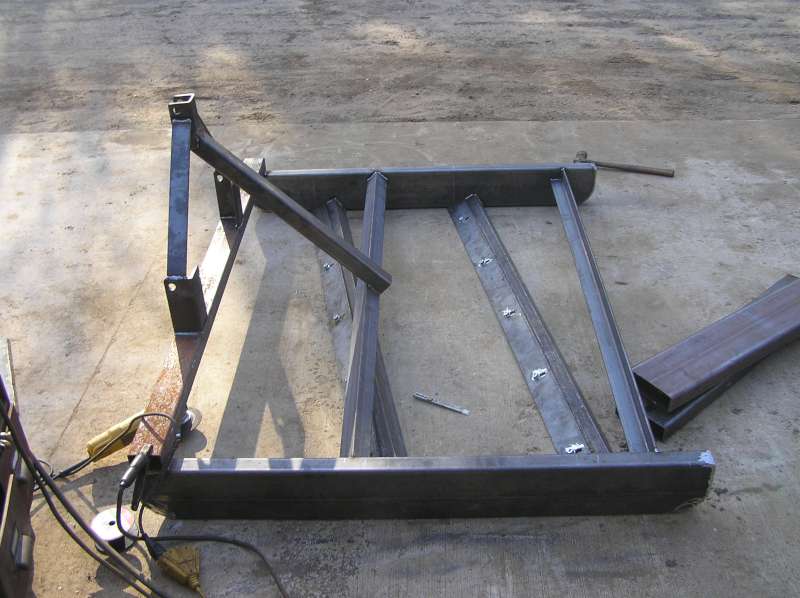
And finally, I turned some pins for the lift arms. Now for some testing and paint:
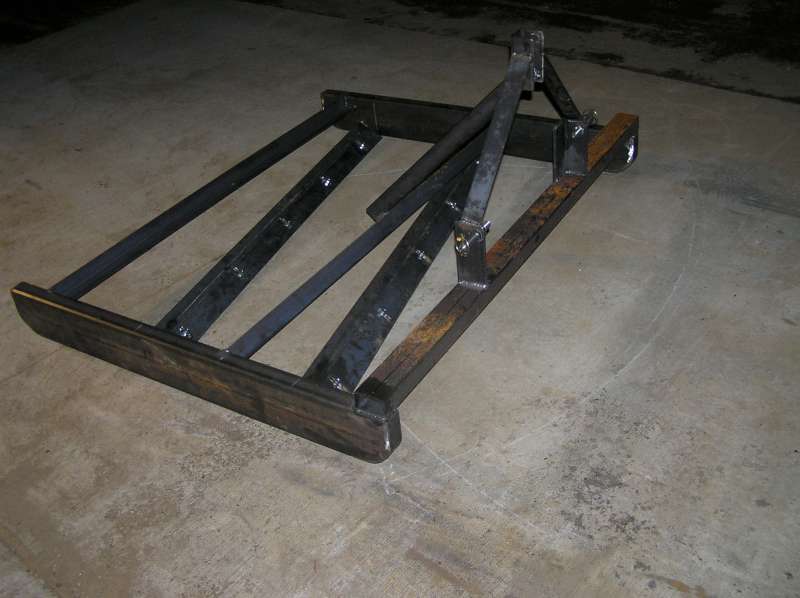