Russell King
Well-known member
Lifetime Member
Equipment
L185F, Modern Ag Competitor 4’ shredder, Rhino tiller, rear dirt scoop
To answer a few of your questions
1) All augers do not attach to the implement in the same manner. Some are round and pinned and others are hex shaped. I also assume that larger implements would have larger diameter shafts on the auger attachment side.
2) There are fairly specific dimensions for the different categories of 3PH with 0 being the smallest size. A cat 2 implement will not fit on a cat 1 3PH. BUT the sizes are sometimes close enough that the implement can be designed for two sizes. For instance I often use Cat 1 implements on my cat 1 3PH tractor but turn the pins inwards to make it work easier.
3) There are longer and shorter augers that will work on the same implement. But if the tractor can’t lift the auger above the ground then that auger is useless for that implement since you can’t get the hole even started. But you can put extensions on the auger when the short auger is too short. But then you have difficulty getting the auger out of the hole and you will need to clean out the hole by hand.
4) There are different types of augers for different types of soils and rock even.
5) 3PH auger are better than hand digging a hole but the will get stuck and you will have to get it unstuck which means either use something like a pipe wrench to unscrew it or dig a hole around the auger by hand. You will som have to adjust the location of your hole to avoid a large rock or resort to digging it out by hand.
6) You will need to clean out loose dirt at the bottom of the hole by hand in every hole to get post to proper depth. The auger just won’t be able to do a good enough job. You can sometimes over dig the depth then fill it back in with a long enough auger or short enough hole.
Hope that helps you some. Just make sure you get a complete PTO shaft with the implement and also that the auger is also included. Many of the new ones have no auger, many of the used ones have only part of the PTO shaft with them.
There is also a method for pounding the post into the ground that is used where the soil allows for that. I don’t think those pounders require too much hydraulic flow so may be suitable for your tractor. But the implement may be expensive. There are some hand held versions but I have no experience with them but they are not too expensive
Look at Kencove for fence material and instructions if you’re new to fence building.
kencove.com
1) All augers do not attach to the implement in the same manner. Some are round and pinned and others are hex shaped. I also assume that larger implements would have larger diameter shafts on the auger attachment side.
2) There are fairly specific dimensions for the different categories of 3PH with 0 being the smallest size. A cat 2 implement will not fit on a cat 1 3PH. BUT the sizes are sometimes close enough that the implement can be designed for two sizes. For instance I often use Cat 1 implements on my cat 1 3PH tractor but turn the pins inwards to make it work easier.
3) There are longer and shorter augers that will work on the same implement. But if the tractor can’t lift the auger above the ground then that auger is useless for that implement since you can’t get the hole even started. But you can put extensions on the auger when the short auger is too short. But then you have difficulty getting the auger out of the hole and you will need to clean out the hole by hand.
4) There are different types of augers for different types of soils and rock even.
5) 3PH auger are better than hand digging a hole but the will get stuck and you will have to get it unstuck which means either use something like a pipe wrench to unscrew it or dig a hole around the auger by hand. You will som have to adjust the location of your hole to avoid a large rock or resort to digging it out by hand.
6) You will need to clean out loose dirt at the bottom of the hole by hand in every hole to get post to proper depth. The auger just won’t be able to do a good enough job. You can sometimes over dig the depth then fill it back in with a long enough auger or short enough hole.
Hope that helps you some. Just make sure you get a complete PTO shaft with the implement and also that the auger is also included. Many of the new ones have no auger, many of the used ones have only part of the PTO shaft with them.
There is also a method for pounding the post into the ground that is used where the soil allows for that. I don’t think those pounders require too much hydraulic flow so may be suitable for your tractor. But the implement may be expensive. There are some hand held versions but I have no experience with them but they are not too expensive
Look at Kencove for fence material and instructions if you’re new to fence building.
Kencove Farm Fence Supplies
Kencove Farm Fence product specialists guide you to the best supplies for your situation. Top Quality, Reasonable Prices, Fast Delivery - we want to make your fence project a fulfilling success.
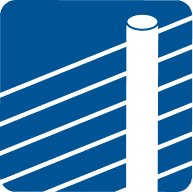