King Kutter Re-design & Repair
Purchased new, This 5 foot King Kutter finishing mower has done O.K. for many years. The wet environment has taken its toll and rust has eaten many areas away.
Besides the rust repairs, the design is very poor resulting in poor cutting results, more like a UN-Finishing mower.
The mower would easily clog in deep and/or wet grass, forcing me to re cut areas several times, so a redesign is a must while I repair the rust damage.
Purchased new, This 5 foot King Kutter finishing mower has done O.K. for many years. The wet environment has taken its toll and rust has eaten many areas away.
Besides the rust repairs, the design is very poor resulting in poor cutting results, more like a UN-Finishing mower.
The mower would easily clog in deep and/or wet grass, forcing me to re cut areas several times, so a redesign is a must while I repair the rust damage.
Re-Designing & Repairing this mower without spending little if any money will take all the scrap metal I have.
I"ll have to use all my ingenuity to take this pile of crap scrap metal and make it into a usable piece's that have form & function.
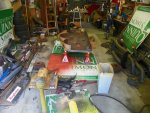
All the rust has to be removed so several wire wheels for my grinder had to be purchased.
After removing all the rust possible I coated the area with a rust inhibitor to stop & prevent further rusting as well as to make it paint-able.
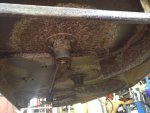
Once that was dry I brushed on a graphite type of paint that will help prevent any grass wet or not, from sticking and causing clogging and clumping.
The support beams really screw up a nice flow, However removing them would compromise structural support. so they will stay for now.
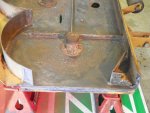
Both metal sides, one of which is the discharge are both rusted through and will need to be replaced.
I actually plan on making both sides discharge in order to prevent clumping, clogging & tracking, due to the current design overwhelming the blades because of the amount of grass its trying to handle.
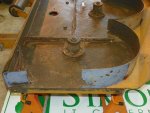
As you can see, this is a feeble attempt at some sort of tunneling. While this design might be ok for a rear discharge mower, as you can see this is a single side discharge mower. this is a must fix issue, if the performance of this mower will ever be at its full potential.
There is about a 4" gap between this retarded partial tunnel design and the blade making it almost useless!
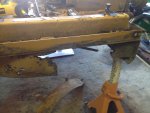
The beginning of the tunnel making, by cutting bending & hammering into shape some scrap metal, in order to form the bottom or back side of my tunnel design.
You can see my first piece in the center bottom above the round hole.
In case you haven"t noticed, the blades have already been modified. This was not easy due to the opposite rotation of the blades compared to the rest of the world, so going to the store and purchasing blades was out of the question.
After many months of searching, I happened across a set of 3 small blades from my old 50s simplicity lawn tractor and to my surprise they also rotate backwards!
As my tunnel design comes together, you can see that I cut the original portion loose and re-welded it a thumbs distance closer to the blade, then began to make the pieces for the bottom side of the tunnel.
Besides the mowers poor condition & performance needing addressing, the method used to pick up my mower also needed redesigning.
With my mower, a single chain & steel strap was bolted to the center rear and to the 3 point hitch, which caused or allowed the mower to fall to one side or the other when lifted.
Not only was this dangerous it was annoying, so I removed the chain & strap crap and made my own double contact lift that lifts the deck in a secure & stable manor. The idea came from this picture I found while surfing Google.
See more pics here
https://www.facebook.com/DIYLASERS/media_set?set=a.10201782981528020.1073741829.1586118119&type=3
Last edited: