I have a tiller that came with my tractor. I was aware a drive chain was broken on the side, but didn't realize the arm that holds the tension spring and sprocket took a blow and was bent. The arm itself is bent, but more importantly, the sidewall of the tiller is a bit twisted, where the connection bolt was attached.
Should I just beat on this steel, I think it is 10-11 gauge, with a sledge to try and flatten? Would it be appropriate to use a torch on this to heat and then hit it? The bend in the tiller sidewall and the arm is causing the arm to not apply tension to the chain, as well as the bolt connecting the arm to the tiller, will hit the chain when in operation and break the chain again, I am afraid. Attached is a shot from the manual with redlines and some photos.
The gears do line up to keep the chain along the same access, but I am pretty sure the bolt hole needs to be flattened at a minimum.
Thanks for any advice!
Manual:
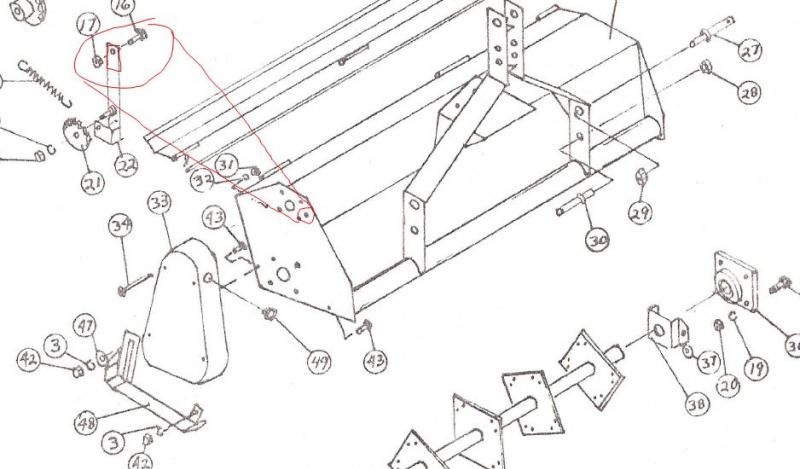
Slight bend in arm:
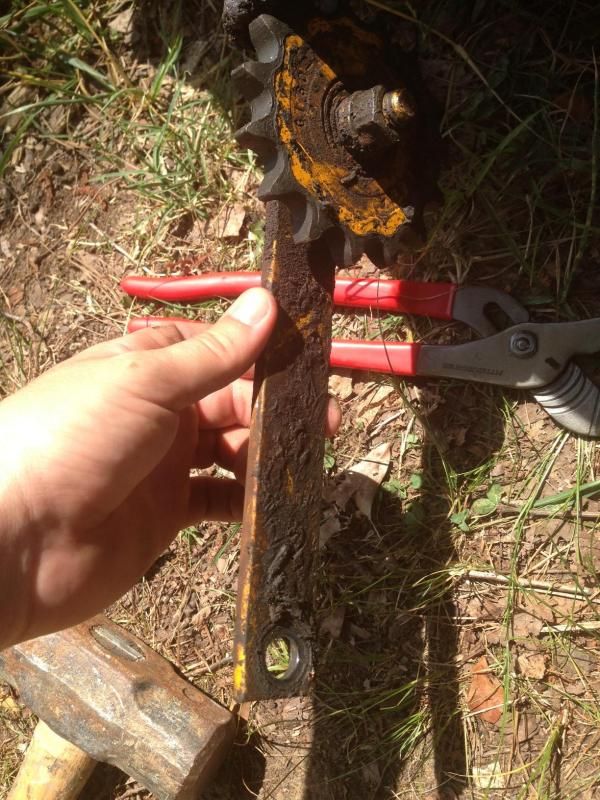
Better View:
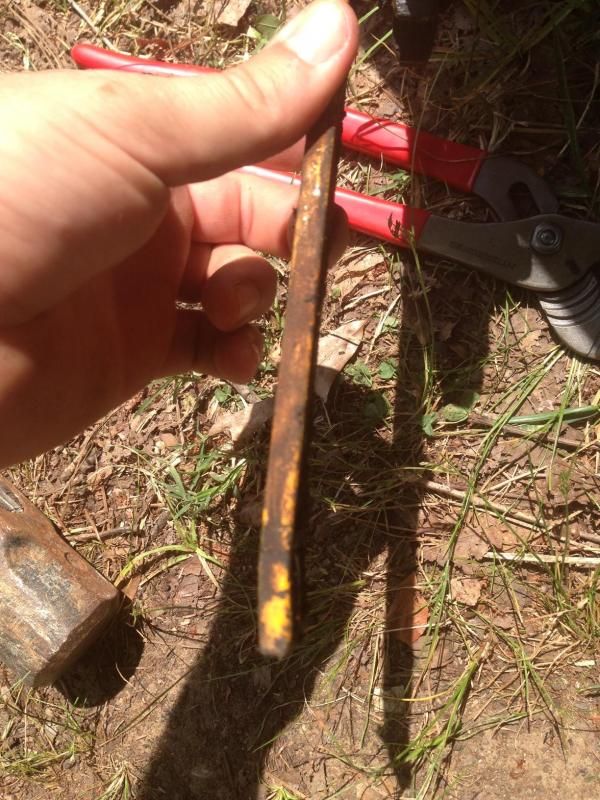
Tiller sidewall bent at bolt hole:
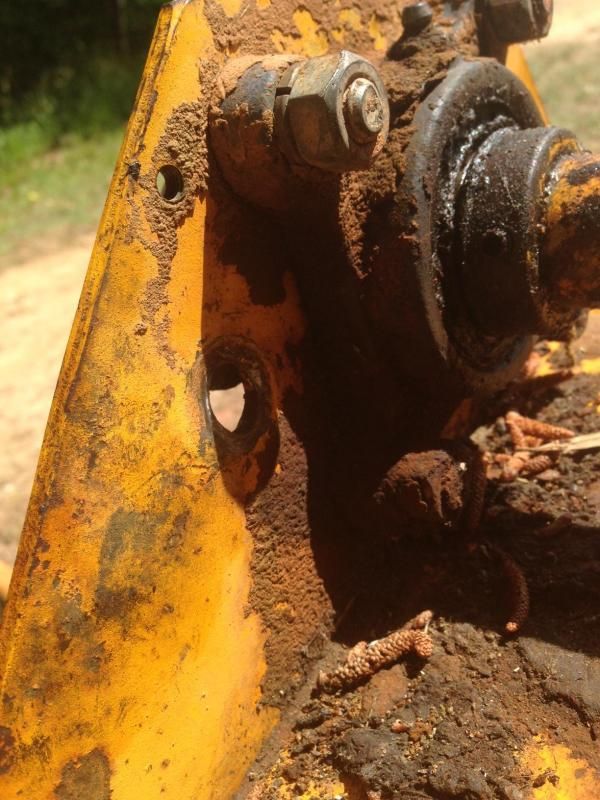
Should I just beat on this steel, I think it is 10-11 gauge, with a sledge to try and flatten? Would it be appropriate to use a torch on this to heat and then hit it? The bend in the tiller sidewall and the arm is causing the arm to not apply tension to the chain, as well as the bolt connecting the arm to the tiller, will hit the chain when in operation and break the chain again, I am afraid. Attached is a shot from the manual with redlines and some photos.
The gears do line up to keep the chain along the same access, but I am pretty sure the bolt hole needs to be flattened at a minimum.
Thanks for any advice!
Manual:
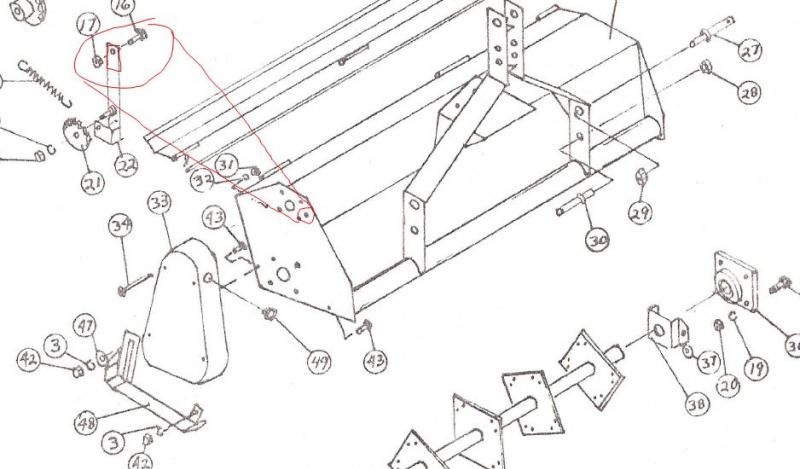
Slight bend in arm:
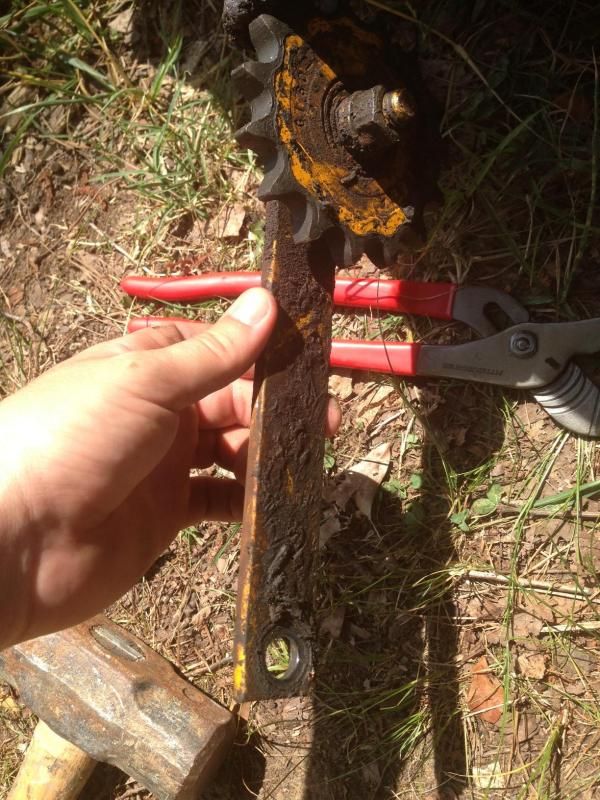
Better View:
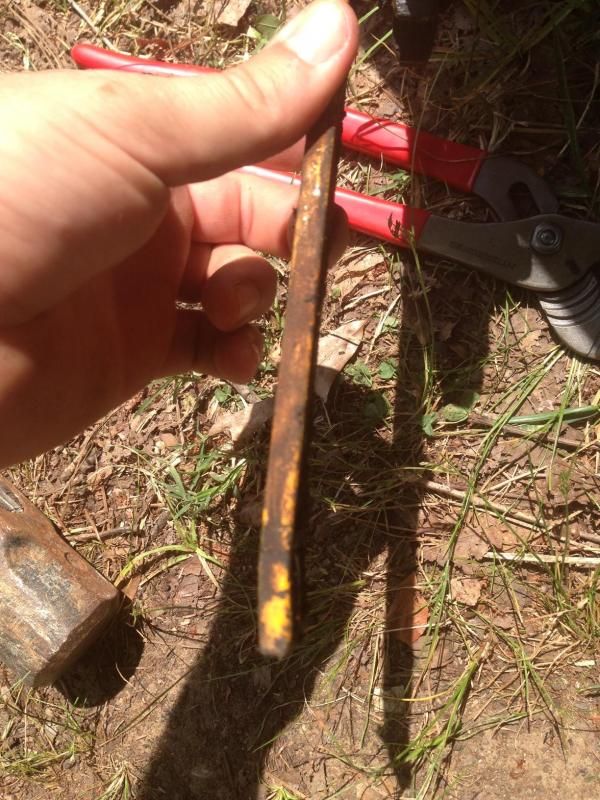
Tiller sidewall bent at bolt hole:
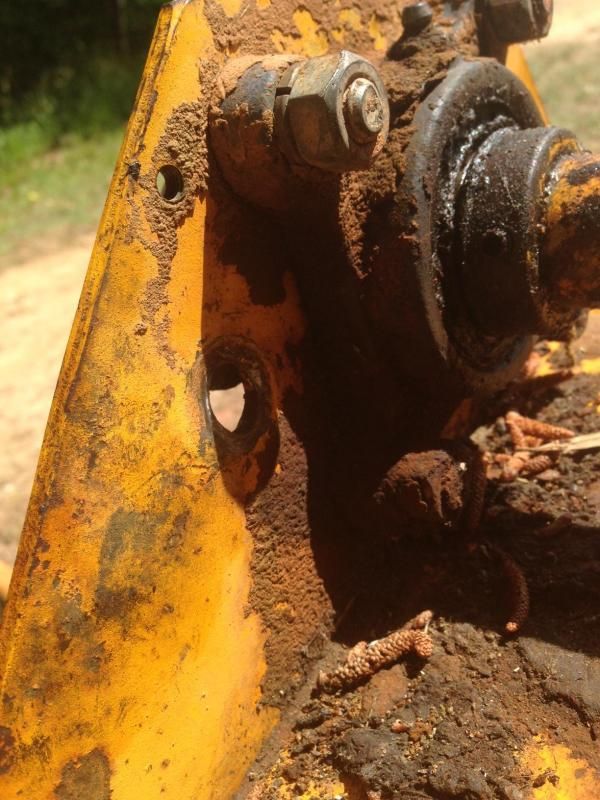